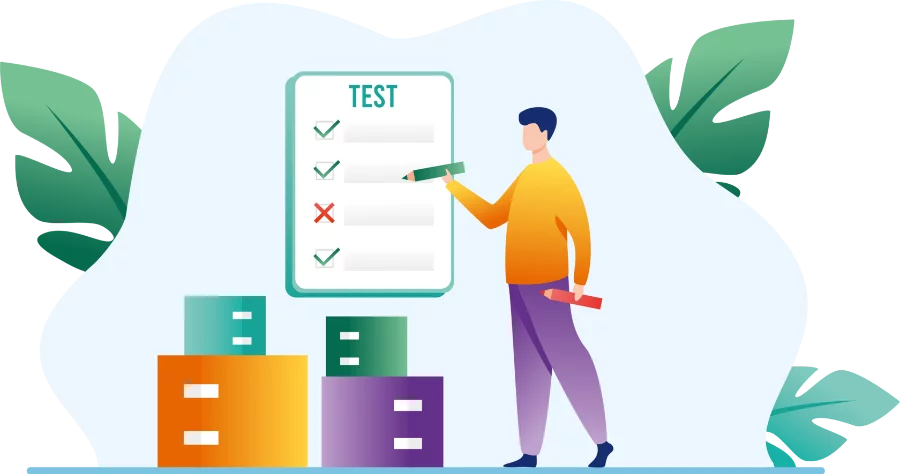
PRE-SHIPMENT INSPECTION
Yuvan Groups conducts Pre-Shipment Inspection (PSI) as one of its many quality control inspections to guarantee that the quality of your product meets your expectations prior to shipment.
What Is Pre-Shipment Inspection?
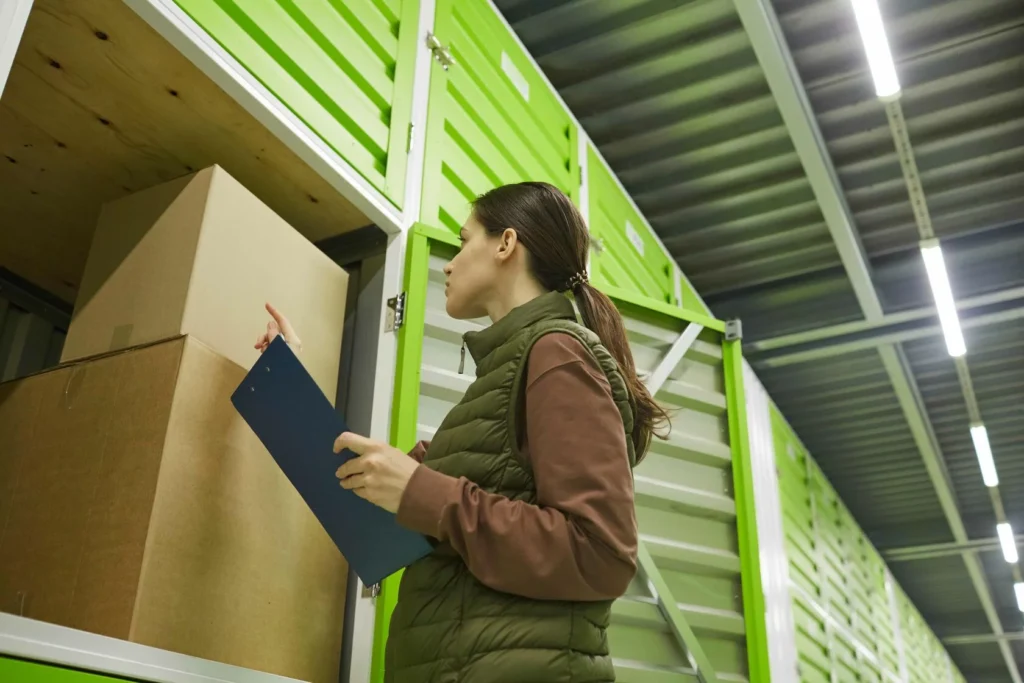
Prior to initiating payment, a pre–shipment inspection allows you to address any problems that may arise. Inspection agencies will scrutinize the items before they are shipped, making it possible for you to withhold the last payment until you get the report and make sure that quality control meets the necessary standards. This process will only take place when 100% of the ordered products have been made and 80% have been packaged to avoid the danger of checking only chosen samples.
Your Pre-Shipment Inspection Checklist
When there are no complications, a pre-shipment inspection procedure is generally straightforward.
1. Strategy
For most common goods, ordering a pre–shipment inspection is optional; however, medical equipment must be inspected in order to comply with international trade standards.
2. Inspector on site
Inspections at the warehouse or production house are usually straightforward when there are no complications prior to shipment.
3.Off-site shipping inspections
A pre–shipment inspection off–site can only be organized for items that necessitate special treatment, such as hazardous materials.
4. Quantity check
The agent verifies the quantity, destination, and condition of the boxes to ensure the accuracy of the number of boxes and items.
5. Randomized sampling
To guarantee that the entire batch meets standards, PSI inspections are conducted on certain items picked at random employing the statistical sampling technique. The number of items to be inspected (the Acceptance Quality Limit or AQL) is typically outlined in the agreement between the manufacturer or importer and the customer.
6. Visual check
When performing a visual inspection, one should check for both possible mechanical damage and errors in production, such as missing screws or gaps between components.
7. Volumetric verification
The inspector then compares the physical characteristics (height, width, length, color, weight, markings, and labeling) with the client‘s required ones.
8. Functionality verification
esting is done on the items to ensure that no functional flaws exist.
9. Safety test
The safety test is composed of two parts: mechanical safety and electrical safety. The mechanical safety checks are done through a PSI inspection to detect any possible hazards, such as sharp edges or blocked moving parts, that could cause injuries. The electrical safety testing, however, is more complicated and requires laboratory–grade equipment and conditions, and is thus rarely done on–site. This testing looks for risks like gaps in ground continuity or power element faults. Additionally, the certification labeling (UL, CE, BSI, CSA, etc.) is inspected to guarantee the electronic parts are meeting the standards of the destination market.
10. Inspection report
The pre–shipment inspection report includes all failed and passed tests, relevant findings, and comments from the inspector, and can be utilized in the event of any disagreements with the manufacturer. It also displays the acceptance quality limit of the production run and supplies an unadulterated status of the shipment to the destination market. Finally, all the data is gathered into the report.